Memry can meet any customer’s requirements with respect to process, final quality, and contract testing/analysis. Standard Nitinol tests such as, but not limited to, Cyclic Tensile Testing, Differential Scanning Calorimetry (DSC), Bend and Free Recovery (BFR) and Cyclic Polarization Corrosion Testing are available upon request, with custom testing methods regularly developed as needed.
Mechanical Testing
In order to characterize net-shape Nitinol material (i.e. wire, sheet, tube, strip, etc.) and finished component functional properties, Memry utilizes several mechanical testing techniques such as tensile testing, 3-point bend testing and low cycle tensile tests.
Tensile testing is the most common method for characterizing the mechanical properties of Nitinol alloys. Tensile testing is used to obtain critical material properties such as the ultimate tensile strength (UTS), elongation to failure as well as the superelastic (or pseudoelastic) upper and lower plateau stresses (i.e. UPS and LPS) per the ASTM F2516 standard.
Mechanical Testing
In order to characterize net-shape Nitinol material (i.e. wire, sheet, tube, strip, etc.) and finished component functional properties, Memry utilizes several mechanical testing techniques such as tensile testing, 3-point bend testing and low cycle tensile tests.
Tensile testing is the most common method for characterizing the mechanical properties of Nitinol alloys. Tensile testing is used to obtain critical material properties such as the ultimate tensile strength (UTS), elongation to failure as well as the superelastic (or pseudoelastic) upper and lower plateau stresses (i.e. UPS and LPS) per the ASTM F2516 standard.
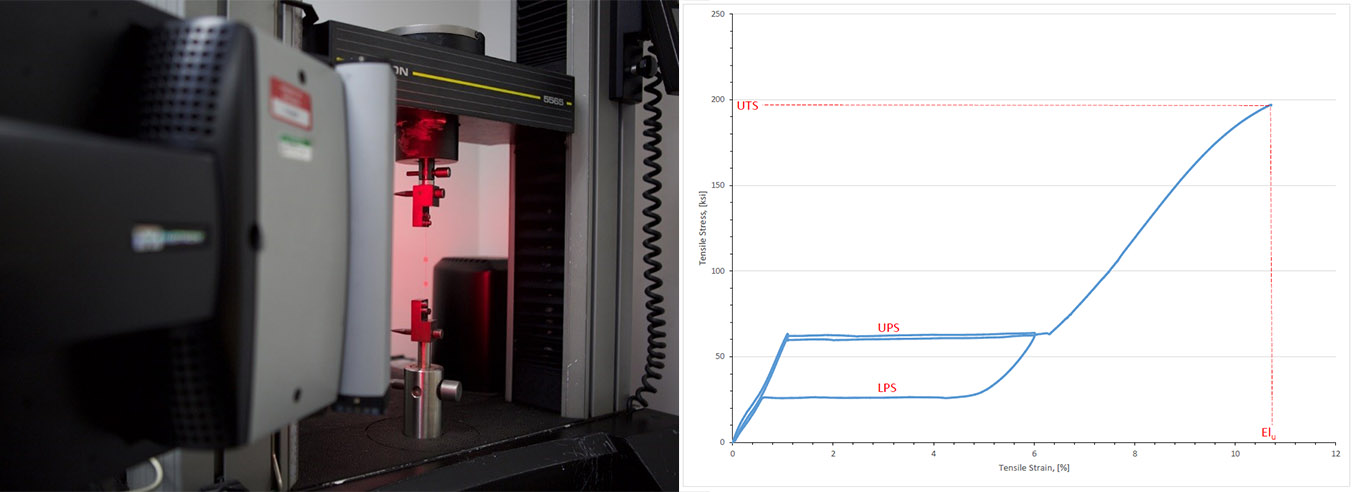
Differential Scanning Calorimetry (DSC)
Differential Scanning Calorimetry (DSC) is a powerful thermoanalytical technique used at Memry for characterizing the phase transformations within a Nitinol alloy. DSC analysis is most commonly used to verify the Ni:Ti ratio of a Nitinol ingot through measuring the Austenite start (As) phase transformation temperature per the ASTM F2063 standard for wrought NiTi alloys. However, DSC curves are also essential in understanding the effects of down-stream thermo-mechanical processes (i.e. cold work, heat treatments, laser processes, etc.) on the Nitinol component functional properties. All DSC tests performed at Memry are ASTM F2004 compliant.
Differential Scanning Calorimetry (DSC) is a powerful thermoanalytical technique used at Memry for characterizing the phase transformations within a Nitinol alloy. DSC analysis is most commonly used to verify the Ni:Ti ratio of a Nitinol ingot through measuring the Austenite start (As) phase transformation temperature per the ASTM F2063 standard for wrought NiTi alloys. However, DSC curves are also essential in understanding the effects of down-stream thermo-mechanical processes (i.e. cold work, heat treatments, laser processes, etc.) on the Nitinol component functional properties. All DSC tests performed at Memry are ASTM F2004 compliant.
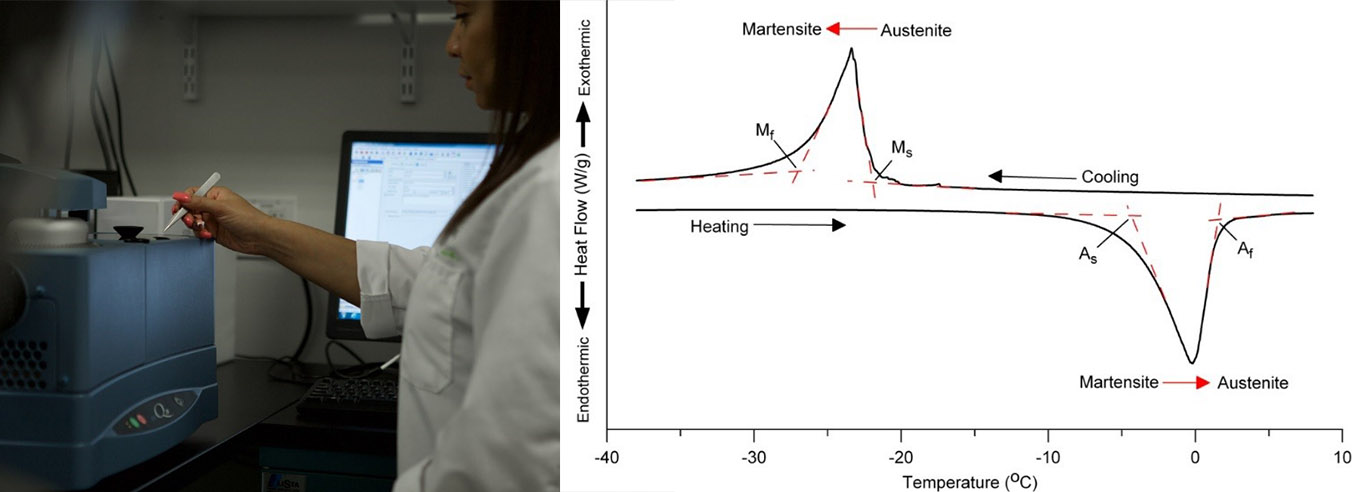
Bend and Free Recovery (BFR)
Bend and Free Recovery (BFR) testing is a non-destructive test used by Memry to identify the Active Af temperature of a Nitinol component. The Active Af temperature is essential for understanding the performance of a device in application while under strain. The Active Af is usually several degrees cooler than the Af temperature measured through DSC testing due to the effects of stress/strain on phase transformations of Nitinol alloys. For this reason BFR testing and the measured Active Af is usually preferred for understanding device performance in application and for final quality verification. All BFR tests performed at Memry are ASTM F2082 compliant.
Bend and Free Recovery (BFR) testing is a non-destructive test used by Memry to identify the Active Af temperature of a Nitinol component. The Active Af temperature is essential for understanding the performance of a device in application while under strain. The Active Af is usually several degrees cooler than the Af temperature measured through DSC testing due to the effects of stress/strain on phase transformations of Nitinol alloys. For this reason BFR testing and the measured Active Af is usually preferred for understanding device performance in application and for final quality verification. All BFR tests performed at Memry are ASTM F2082 compliant.
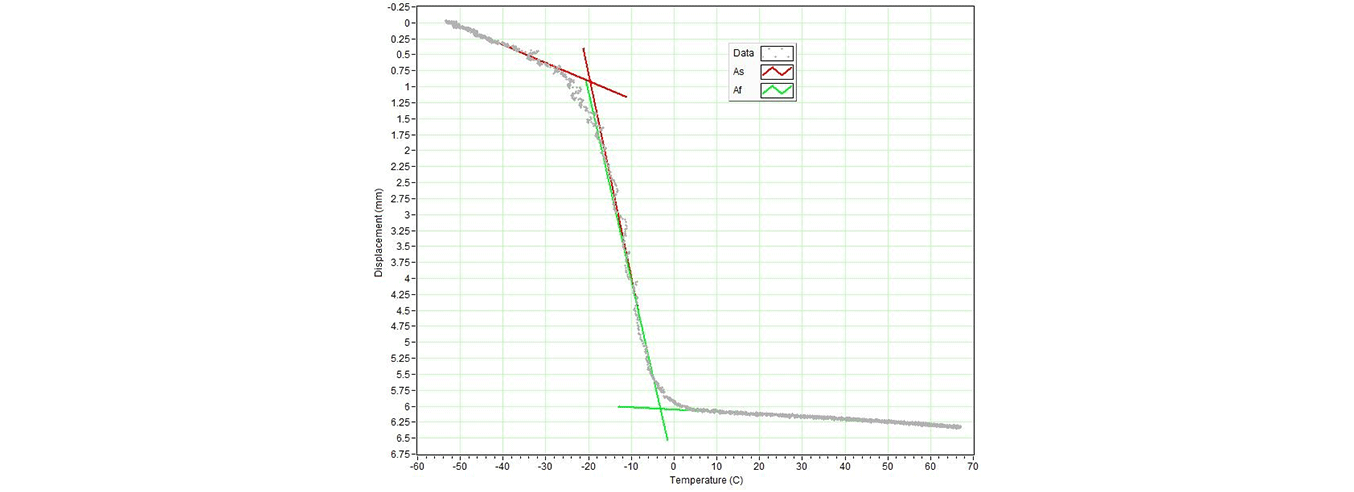
Cyclic Potentiodynamic Polarization Corrosion Testing
Corrosion resistance is critical for Nitinol medical device components. Cyclic Potentiodynamic Polarization Testing is used by Memry to quantify the corrosion resistance of Nitinol components. Up-stream processes such as heat treatments, chemical etching, electro-polishing and surface passivation can greatly affect the resistance of the Nitinol component to pitting corrosion. Cyclic Potentiodynamic Polarization Testing per the ASTM F2129 standard is used to identify properties such as the rest potential (Er), breakdown potential (Eb), and protection potential (Ep).
Corrosion resistance is critical for Nitinol medical device components. Cyclic Potentiodynamic Polarization Testing is used by Memry to quantify the corrosion resistance of Nitinol components. Up-stream processes such as heat treatments, chemical etching, electro-polishing and surface passivation can greatly affect the resistance of the Nitinol component to pitting corrosion. Cyclic Potentiodynamic Polarization Testing per the ASTM F2129 standard is used to identify properties such as the rest potential (Er), breakdown potential (Eb), and protection potential (Ep).
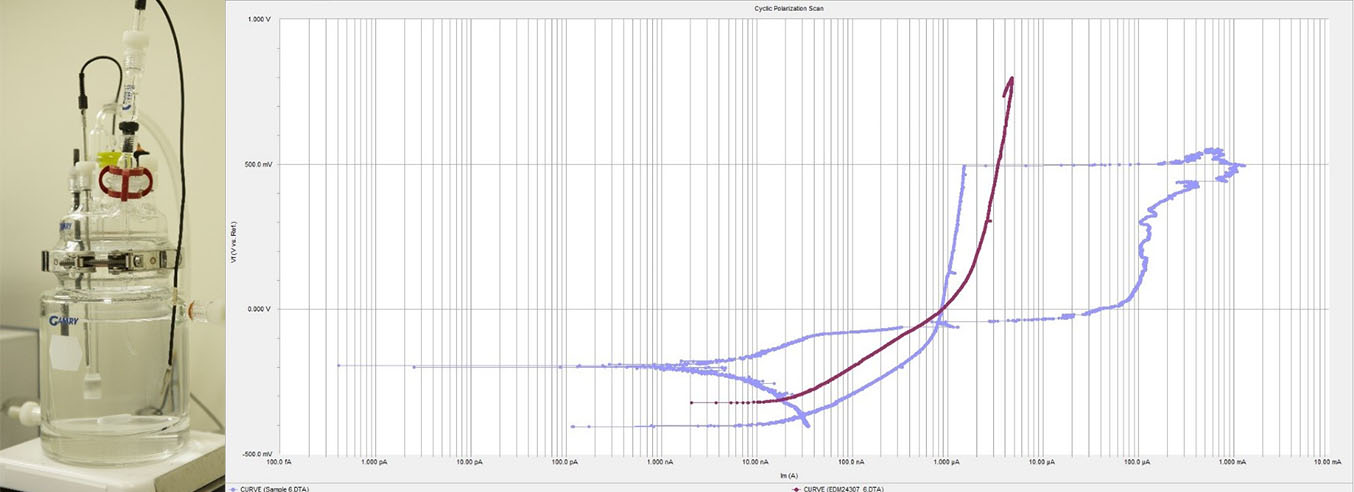
Microscopy
Metallographic sample preparation and microscopy are necessary for understanding the process-structure-performance relationship for a given Nitinol component. Memry utilizes optical and Scanning Electron Microscopy for analyzing metallographic samples. Common metallographic analysis techniques performed include grain size determination, inclusion analysis, weld penetration depth, heat affect analysis (i.e. from laser, EDM cutting, etc.) and failure analysis.
Metallographic sample preparation and microscopy are necessary for understanding the process-structure-performance relationship for a given Nitinol component. Memry utilizes optical and Scanning Electron Microscopy for analyzing metallographic samples. Common metallographic analysis techniques performed include grain size determination, inclusion analysis, weld penetration depth, heat affect analysis (i.e. from laser, EDM cutting, etc.) and failure analysis.
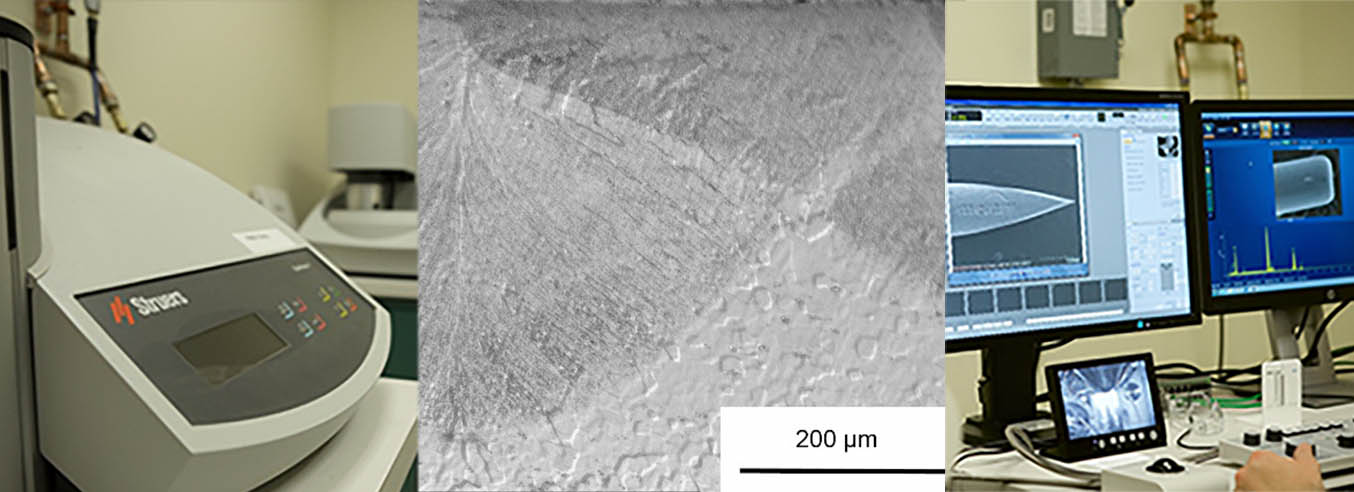
Additional Capabilities
Memry has several other testing capabilities that range from chemical analysis to fatigue testing. Some of these additional capabilities are listed below. Moreover, custom experiments and test set-ups for measuring specific functional properties or operational stability can be designed on a case by case basis.
Memry has several other testing capabilities that range from chemical analysis to fatigue testing. Some of these additional capabilities are listed below. Moreover, custom experiments and test set-ups for measuring specific functional properties or operational stability can be designed on a case by case basis.
- Failure Analysis
- Inclusion Analysis
- EDS Compositional Analysis
- Chemical Analysis (i.e. oxygen, carbon, and hydrogen content)
- Fatigue Testing (e.g. rotating beam test)
- Surface Analysis and Roughness
- Precision Measurement